The fibrous tectonics studio investigates new methodologies, arrangements, and applications of composite-fiber materials, namely carbon and glass fibers which are saturated in epoxy resin. The aim of the investigation is to propose an innovative system of deploying these specific materials.
Our system combines the traditional textile technique of knitting with inflatable pneumatic membranes to create composite-fiber structures. We see these two techniques as inherently complementary. The pneumatic membrane can pretension the fibers of the knit surface and expand it into a spatial and form-active volume while knitting allows the fibrous surface to be behaviorally and topologically programmed, which, in turn, determines how the pneumatic membrane inflates. The resulting configuration of fibers is then saturated with resin and cured into a rigid structure.
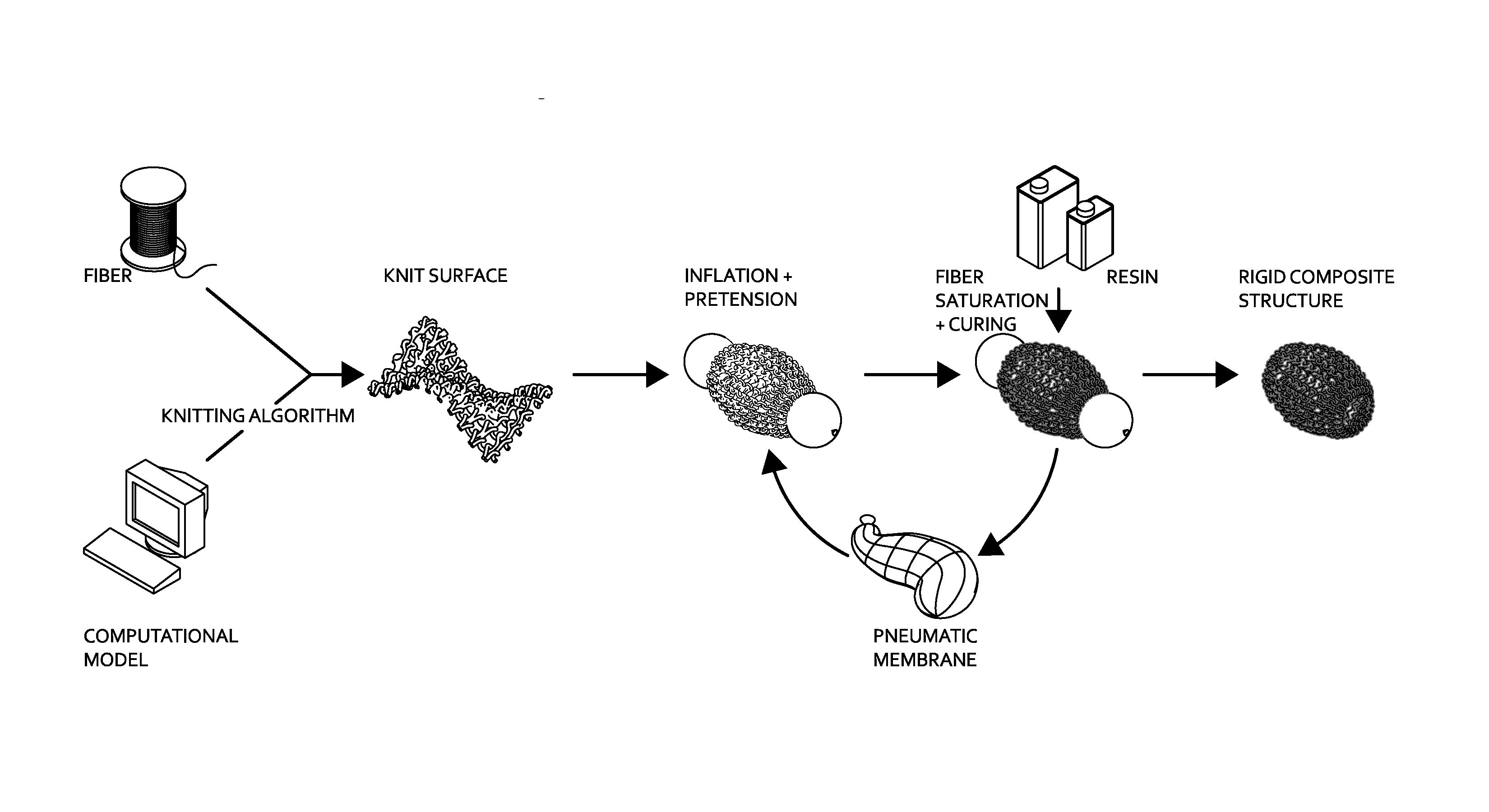
This system addresses three major issues in the contemporary application of composite-fibers. First, composite-fibers today are most often applied as a homogenous, anisotropic surface. Fibers are woven into regular textiles or cut and sprayed in a random (approximately homogenous) configuration. This is a misuse of fibers which have definite isotopic properties and should be deployed efficiently (i. E. Not homogeneously, but where loads [or aesthetics] dictate). Second, conventional processes compromise the continuity (and furthermore the structural integrity) of fibers by cutting textiles into templates or use cut to length fibers in spray applications. The result of these processes are often components that are joined using alien hardware (nuts and bolts). Third, almost all fibers are deployed with the use of a mold or mandrel or scaffold. These aids to production require significant material investment often surpassing the cost of fibers and resin (unless production number per mold is high) and limit the complexity and variety of forms produced.
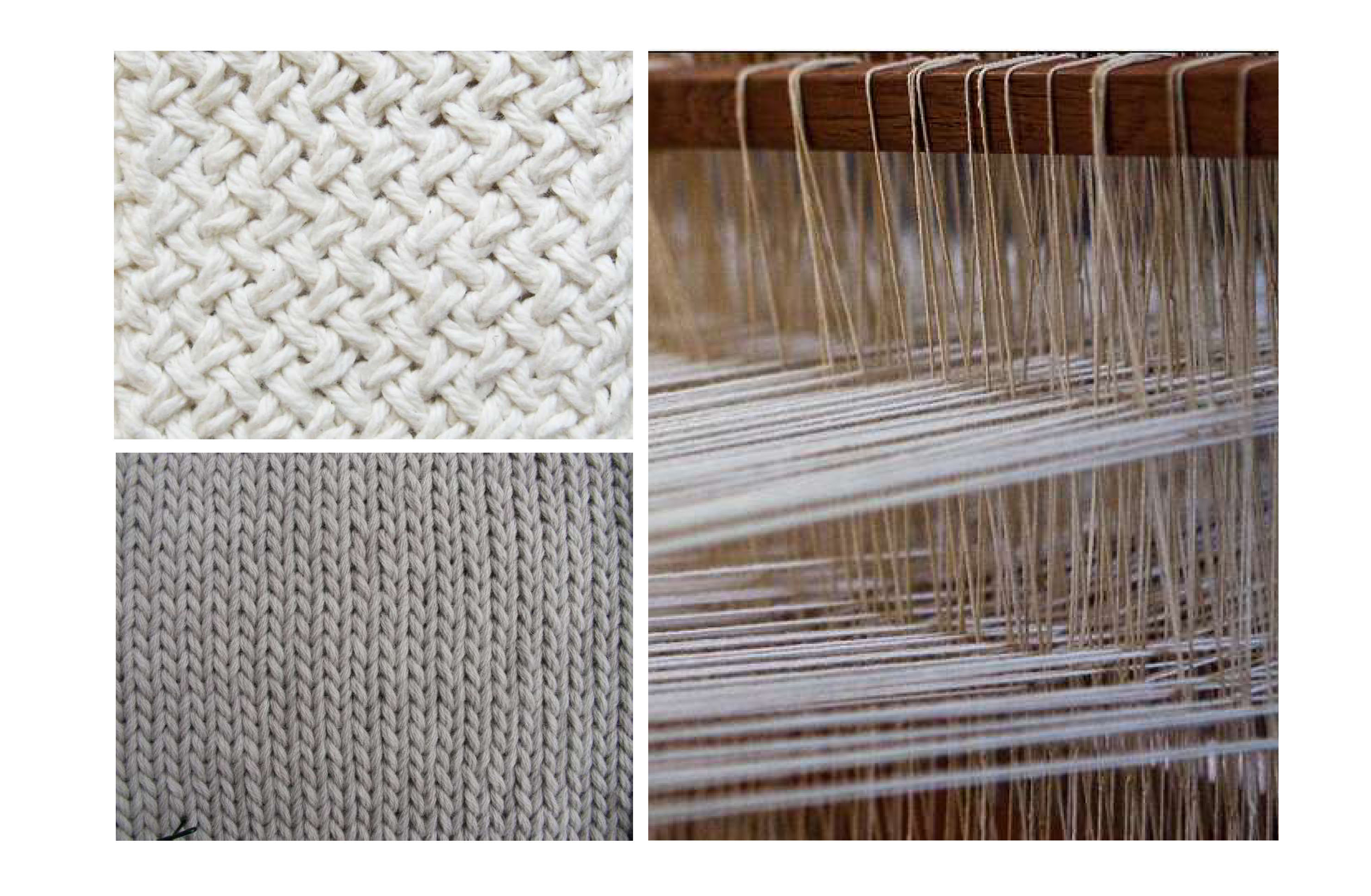
Although the exploration of fibrous-composites such as carbon-fiber and fiberglass is relatively new (1930s), the history of fibrous tectonics is ancient. The notion of making with a fibrous material is heavily rooted in textile traditions. Knitting takes advantage of the anisotropic (and otherwise specific) nature of fibers and is capable of deploying material in a highly programmed heterogeneous arrangement, allowing the designer to control both form and material behavior.
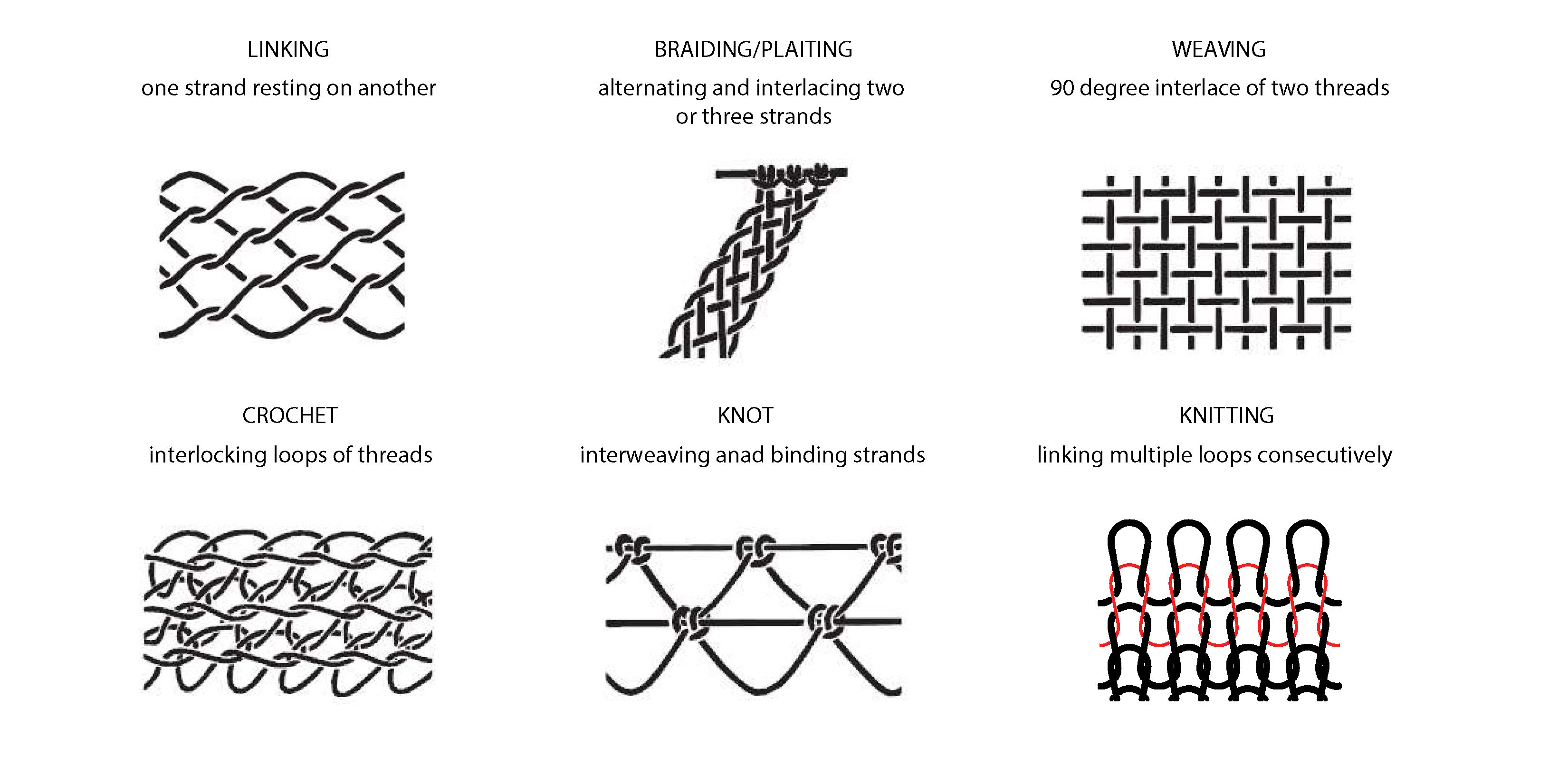
Knitting is an inherently programmable process. The algorithm which informs stitches may allow for a variety of patterns. Alternating the pattern, density, or tension of stitches results in a fabric surface with specific behavioral properties. Elasticity or rigidity, density or porosity can be programmed into the material via geometric arrangement. In this way a highly inelastic material (carbon-fiber) can be rearranged at a tectonic scale to mimic otherwise alien material properties (elasticity). This geometric elasticity can be witnessed in most loose knit clothing. For example, a scarf can have much more elastic than an individual length of yarn from which it is knit. Knitting as a fabrication process allows for material to be deployed in an extremely heterogeneous and specific arrangement, contrasting the homogenous and anisotropic application of conventional processes.
Unlike other textile techniques, knitting uses a single, continuous fiber. Composites function best when fibers are continuous. This configuration of continuous, interlocking loops has the added benefit of allowing the fiber to be easily recycled. Knitting also controls the profile of the resulting surface through the stitch pattern. This contrasts methods such as weaving, where looms are often set to produce rectangular lengths of fabric which are then cut into templates to be assembled, compromising the continuity and integrity of fibers at the edges. Knit surfaces may have complex profiles and topologies where fibers are always continuous at the edge.
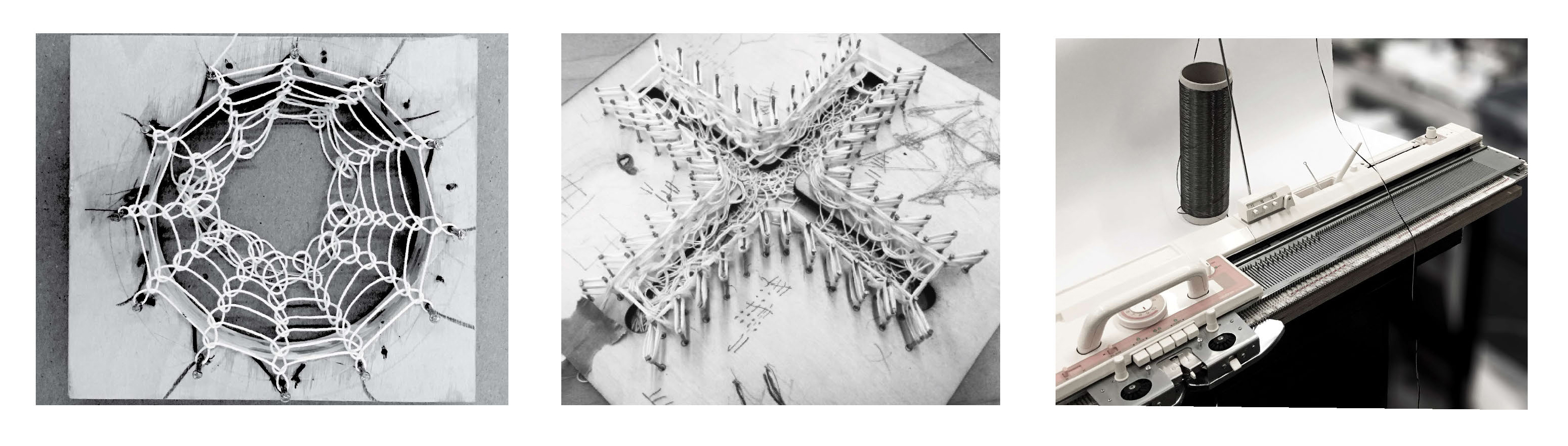
Formal and structural investigations led to the modeling of complex forms and topologies. These would often be approximated by joining several knit-textile surfaces which were produced separately. An incredible benefit of the process is that separate knit surfaces may be continuous/seamless when joined. Stitches identical to those used in the production of the fabric surface may be used to close seams, ultimately creating a uniform condition. Locating seams appropriately allows for complex geometry to be unrolled into manufacturable templates with minimal distortion. Additional information such as stress mapping and load flows may be unrolled along with these surfaces, informing the template's knit algorithm in terms of density and pattern. Ultimately, complex configurations of fibers may be accomplished as tectonically continuous forms, improving upon processes that cut and compromise the integrity of fibers, and component-based systems that rely on alien hardware for aggregation or assembly.
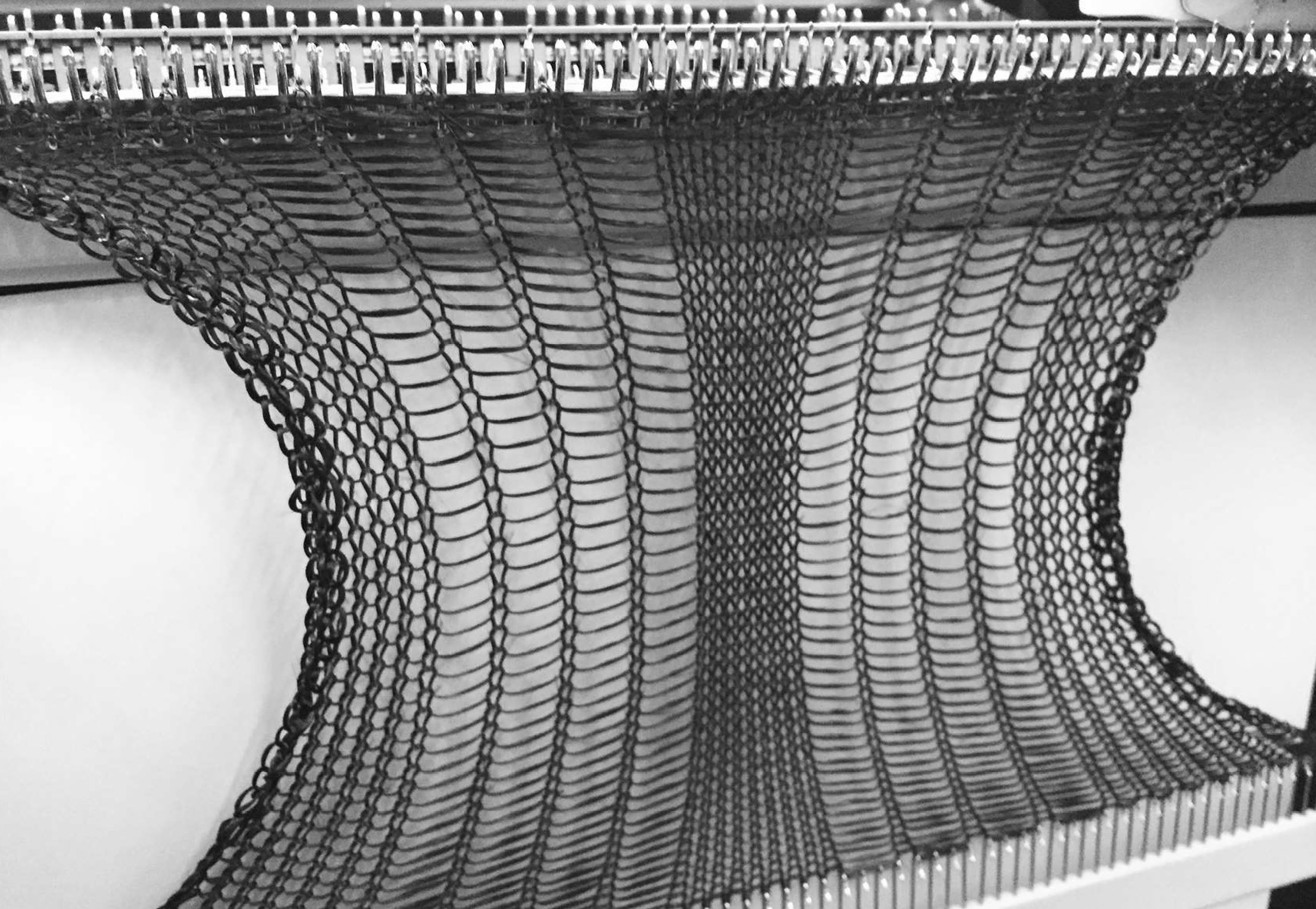
Although knitting affords tremendous possibilities in the deployment of these materials, interacting fibers may only form a tensile surface, and therefore need a means of activation in order to be deployed as a tensioned volumetric form. Fibers can be formed and tensioned within a mold or by winding fibers across the surface of a mandrel or scaffold. Our system investigates tensioning fibers via pneumatic bladders which are inflated inside a (closed) knit surface. Pneumatics require the least material investment per volume of any activation (i. E. Forming and pre-tensioning) system and may be easily scaled.
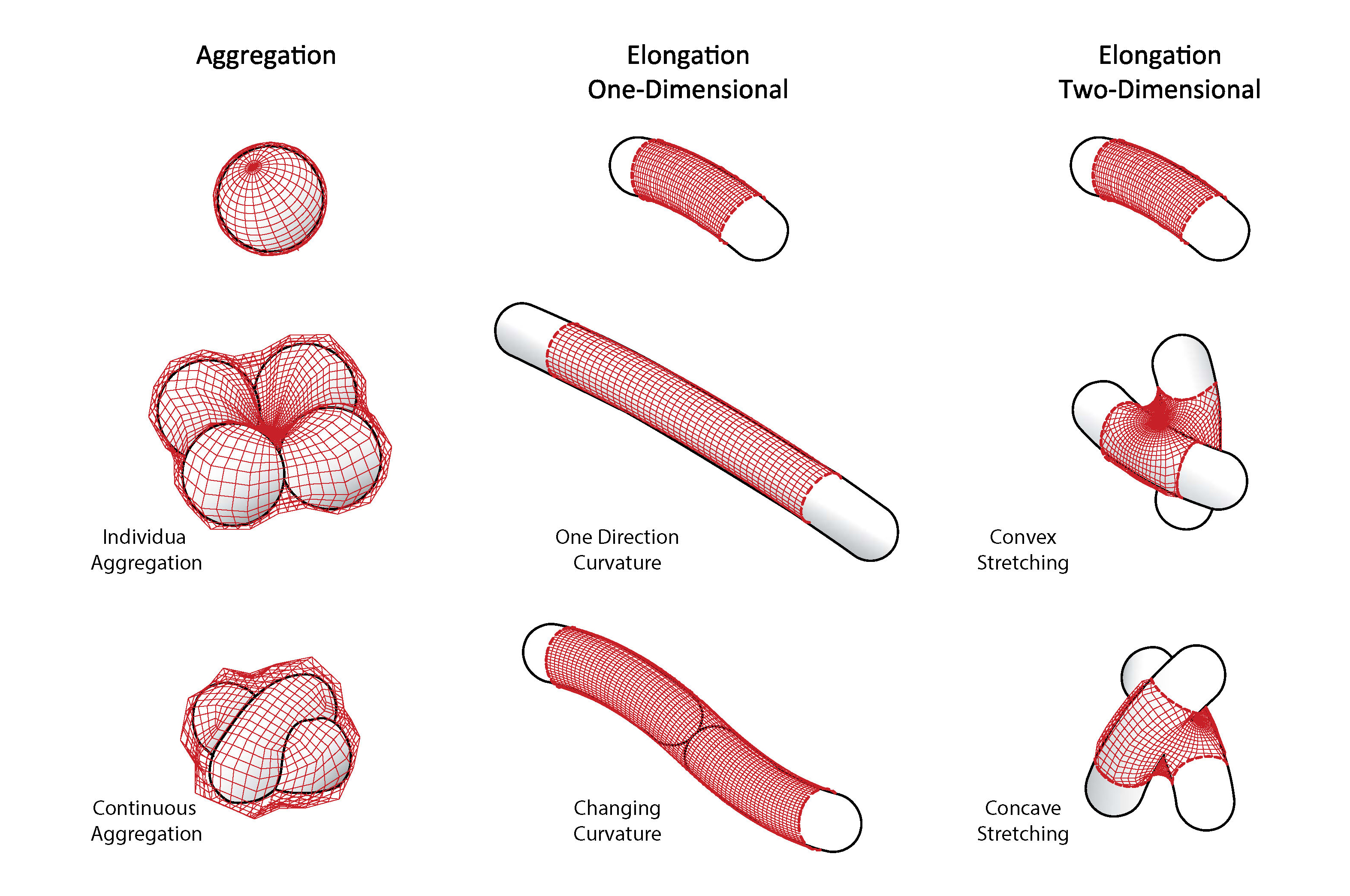
The main reason for abandoning the use of scaffolds was the relatively large material investment and the consequential realization of scale limitations. Pneumatics on the other hand require the least material investment per volume of an 'activation' (i.e. forming and pretensioned) system and may be increased in size either by direct scaling (e.g. Anish Kapoor) or by number in a specifically arranged aggregation.
Since the pneumatic membranes are relatively flexible and malleable, a single type of membrane can be manipulated into a variety of forms by a programmed, enclosing tensile surface. Flexibility / formability (relationship of knit surface to pneumatics) formation/tension.
We began to look at using the knitting techniques we've developed as a means to create a predetermined form. By varying the knitting pattern and technique we are able to program different forms, apertures and openings with in the structure. By finding the code of each form we can begin to manipulate them and establish varying formal algorithms.
Regular standardized pneumatics can be arranged in a controlled way to achieve a variety of unique volumetric configurations. Complexity and uniqueness is a free consequence of the knitting algorithm. In other words, the pattern and topology with which a fibrous textile is knit will pre-determine the form, behavior, and configuration of the interacting pneumatics and fibers.
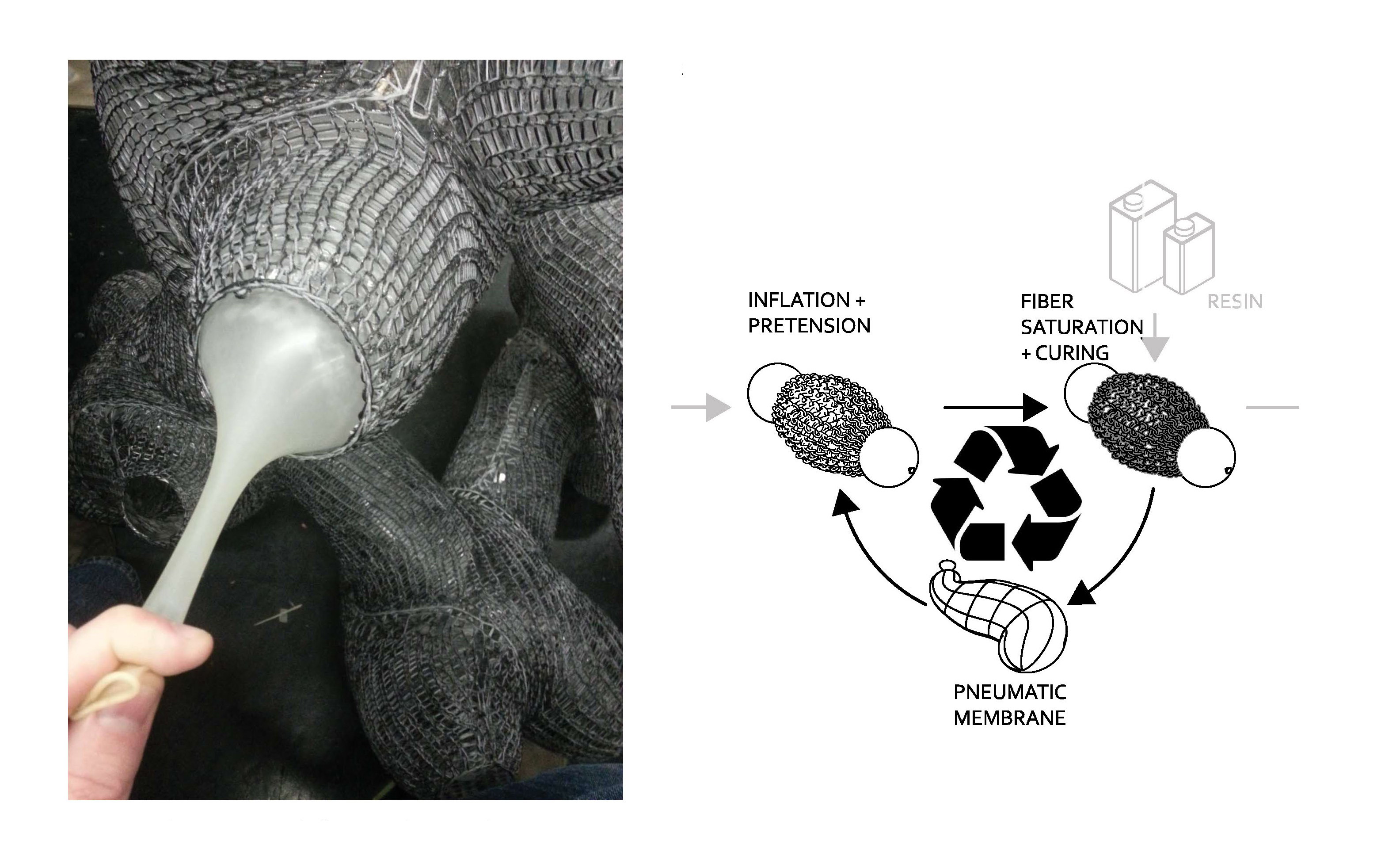
Using regular bladders, knit surfaces can produce a variety of forms and configurations of aggregations. The pneumatic membrane is able to pre-tension the fibers of the knit surface and expand it into a spatial and form-active volume while a knit surface may determine how the pneumatic membrane inflates and aggregates. Complexity and customization are therefore a free consequence of the algorithmic (and possibly automated) knitting process.
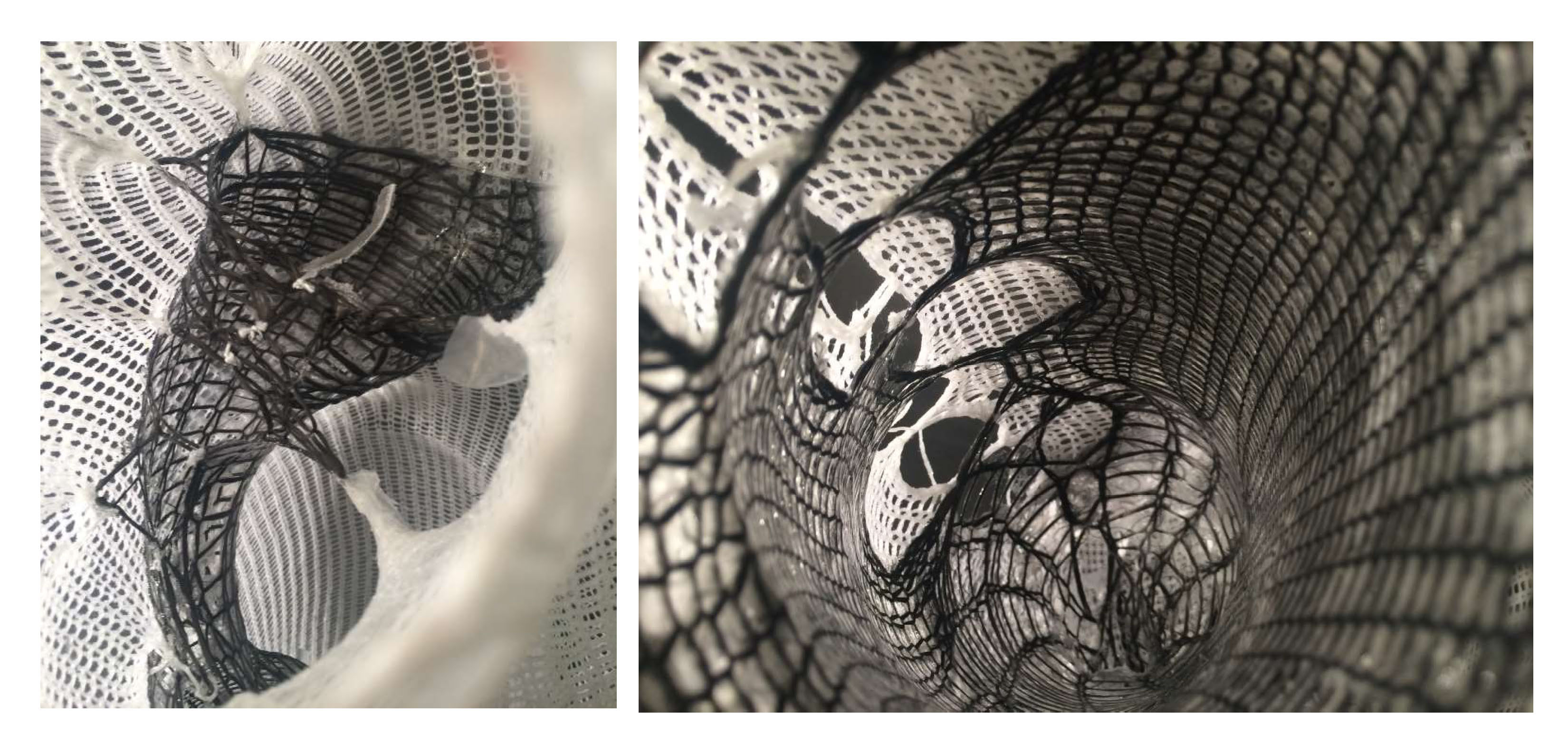
The techniques of knitting and pneumatic inflation are inherently complementary. The pneumatic membrane is able to pre-tension the fibers of the knit surface and expand it into a spatial and form-active volume while a knit surface may determine how the pneumatic membrane inflates and aggregates. Complexity and customization are therefore a free consequence of the algorithmic (and possibly automated) knitting process. This opens possibilities beyond the constraints of the traditional mold. We investigated how these processes allow for a continuous aggregation of fibers that do not rely on the traditional notion of joinery or hardware (which often produce structural weak points in composite structures). Lastly, all processes we have identified have counterparts at a much larger scale, and therefore invite the notion of a scalable system that can approach an architecture.
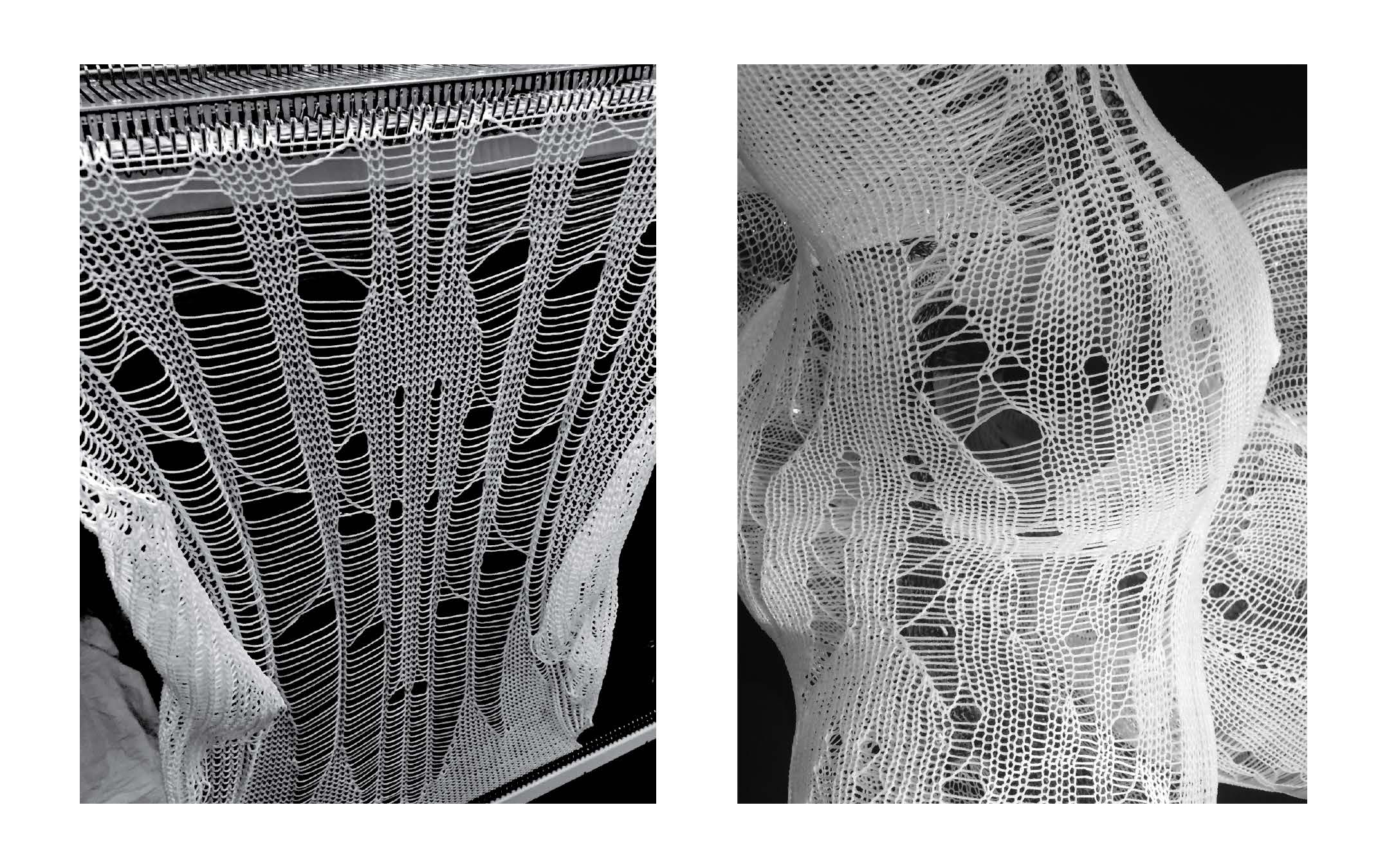
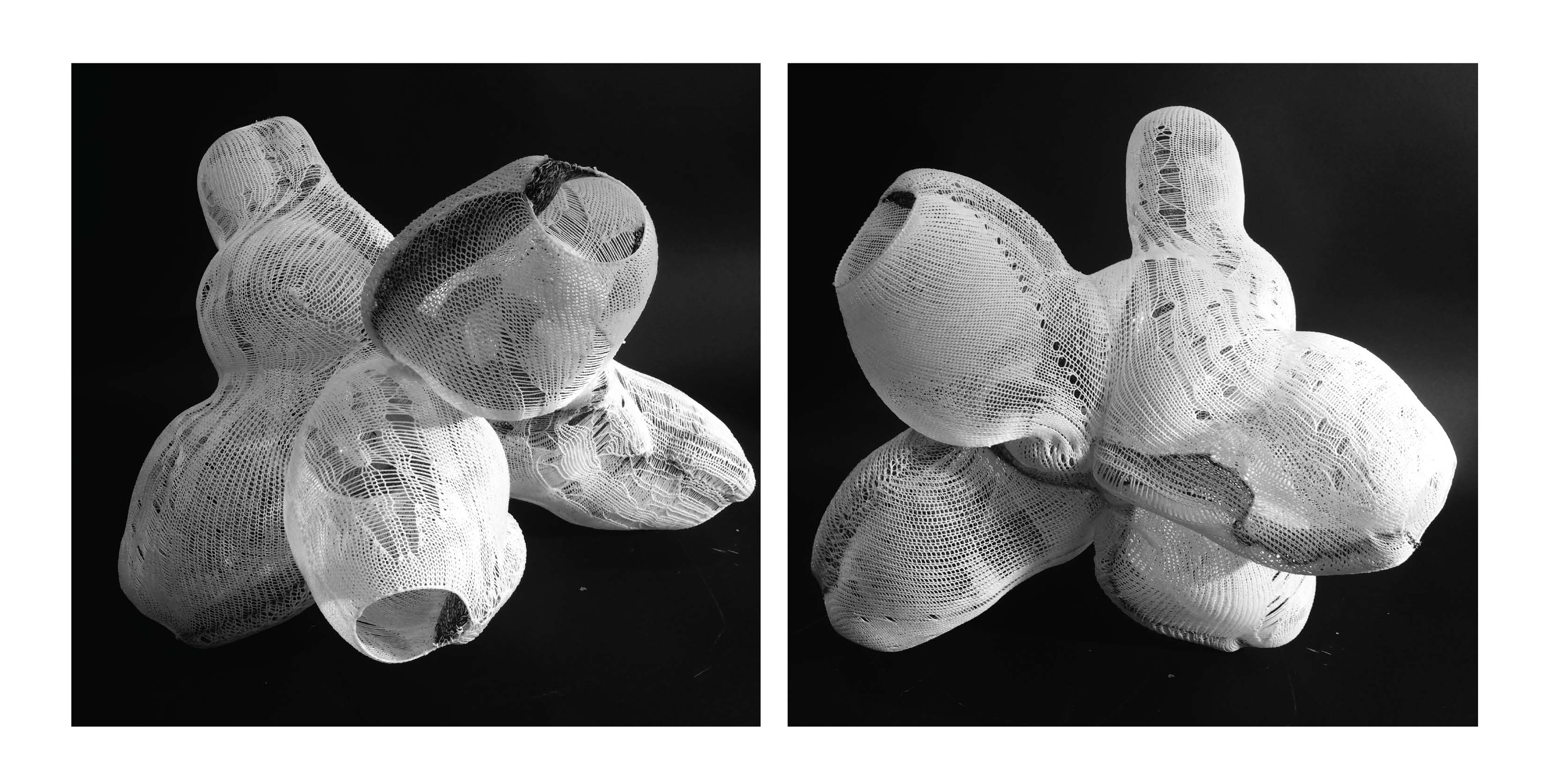
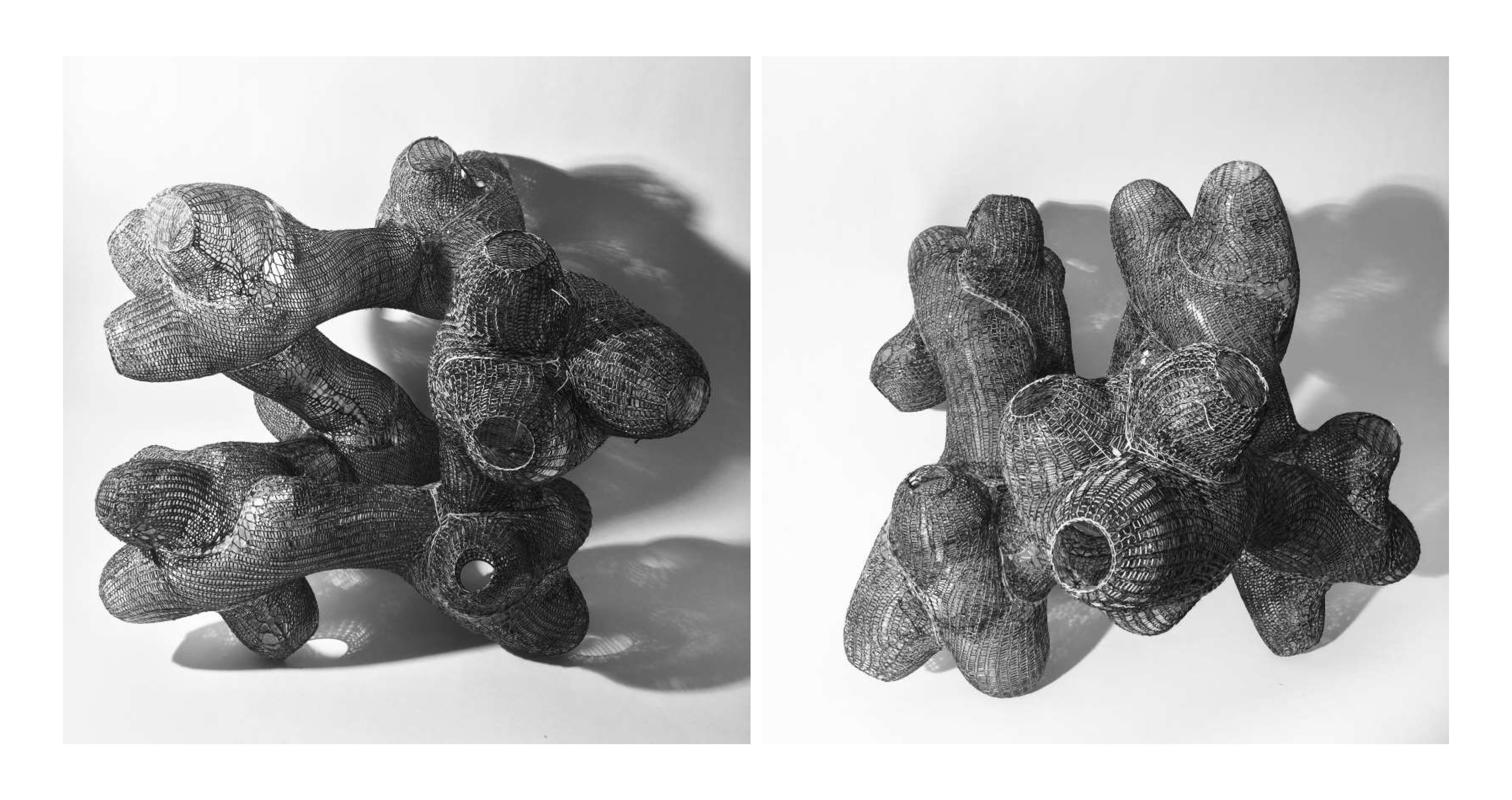
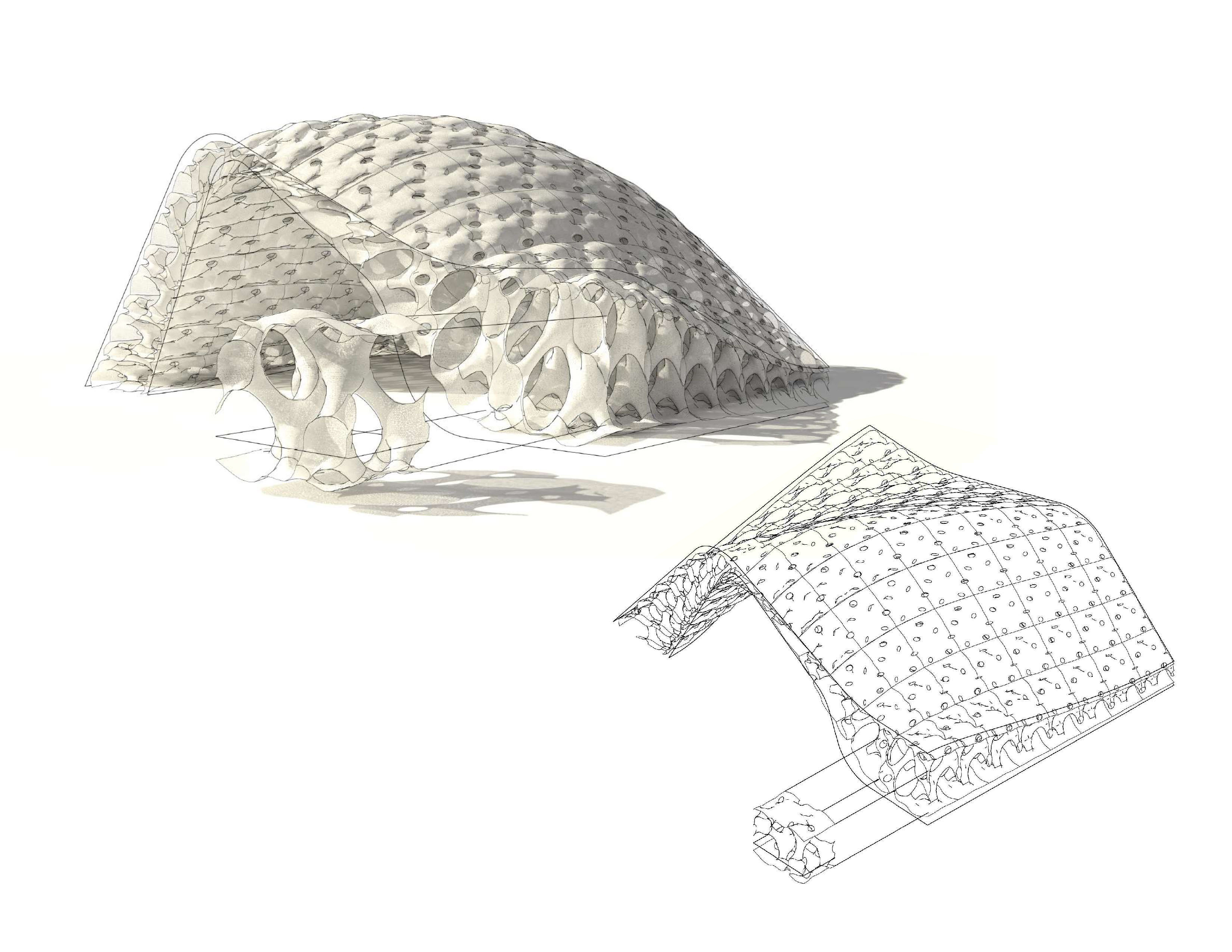
In conclusion, our system combines the traditional textile technique of knitting with inflatable pneumatic membranes to create composite-fiber structures.
“The best work of Achim Menges and colleagues, including that in Menges's design studios on fibrous tectonics at GSD, comprises the most advanced and groundbreaking efforts to break away from the historical tendency to see technological improvements change tools and methods but lead to "little more than transferring traditional [... ] procedures to the operation of machinery.” Specifically, when Purisic, Varholick, Gao, and Safaverdi in the 2015 GSD studio experiment with traditional knitting techniques in a dynamical relation with pneumatic membranes, they succeed in tapping into the power of textile mechanics and geometry to produce startlingly beautiful and fresh architectural effects.” – Johan Bettum